Spinner
Spinning is the process of shaping flat metal into a hollow item using a lathe to spin the metal sheet whilst shaping it over a wooden, nylon or metal former.
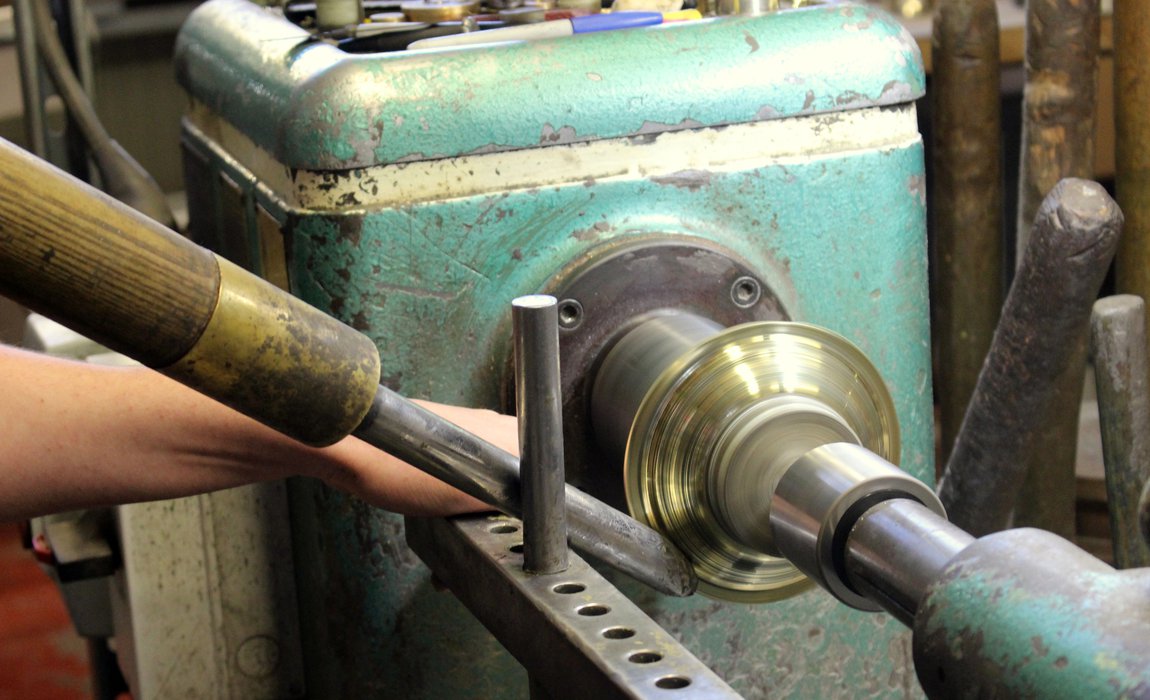
Spinning produces three-dimensional hollow-ware items such as trophies, vessels and cups. Items can be made to varying scales, in quantity, in a uniform and quick way. Spinners also produce and maintain the associated tools, machinery, formers and chucks used to produce spun vessels.
“The body of most trophies are made by spinning including the Musketeer’s Cup, awarded to the winner of the men’s French Open Tennis singles at Roland Garros since 1891.”
What personal attributes are useful for a spinner?
To be a spinner you need to be:
- Interested in working with metals
- Good at working with your hands
- Meticulous
- Comfortable working in a noisy environment
- Able to handle the physical nature of the job – spinners often lever their own weight to push the metal around a former
- A good listener – you might be working to a customers’ designs and you will need to understand what there are looking to achieve and advise them on how to do it
- Trustworthy – you will might be working with someone else’s pieces
- Safety conscious as you will be working with dangerous machinery
It takes practice and years of experience to learn to spin metal. Spinners understand how different metals behave and are very skilled at looking at designs and understanding how best to achieve the required form. To be a successful spinner you will need to be methodical and consistent in your approach and able to produce tooling with an engineer's precision.
What will my working life be like as a spinner?
A spinner will work in a workshop, using a lathe. You can either be employed to work for a company or self-employed. If you work for a company you are part of a bigger team, earn a wage and have standard hours, normally from Monday to Friday. Some spinners will be self-employed or own their business, the hours worked will depend on the volume and type of commissions. Good business, finance and interpersonal skills will be essential.
Within your work you must be able to adhere to industry health and safety requirements; understand the safe storage, handling and disposal of harmful chemicals used in the workshop including the risks involved; know how to safely operate, produce and maintain your machines and tools; the importance of wearing Personal Protective Equipment including safety glasses and ear plugs; and learn how to adequately process your materials.
As a spinner you will use skills and techniques including spinning items in accordance with drawn, verbal or written Instructions to the dimensions given; applying relevant spinning skills and manufacturing techniques using the material supplied; working out materials required for projects; drilling; taping; turning; making section chucks; spinning, annealing; hand forging; hardening and tempering.
You can expect to work with wood; aluminium; nylon; brass; silver; gold; gilding metal; copper; and tool steel. And you will learn how to use tools including measuring and marking out tools; a lathe; shears and guillotines; forging tools; files; sand papers; a blow torch; hand forged spinning tools; formers; wood turning tools; and handmade turning tools. You should receive training in all of these as required.
A day in the life of a spinner - Varis Prieditis
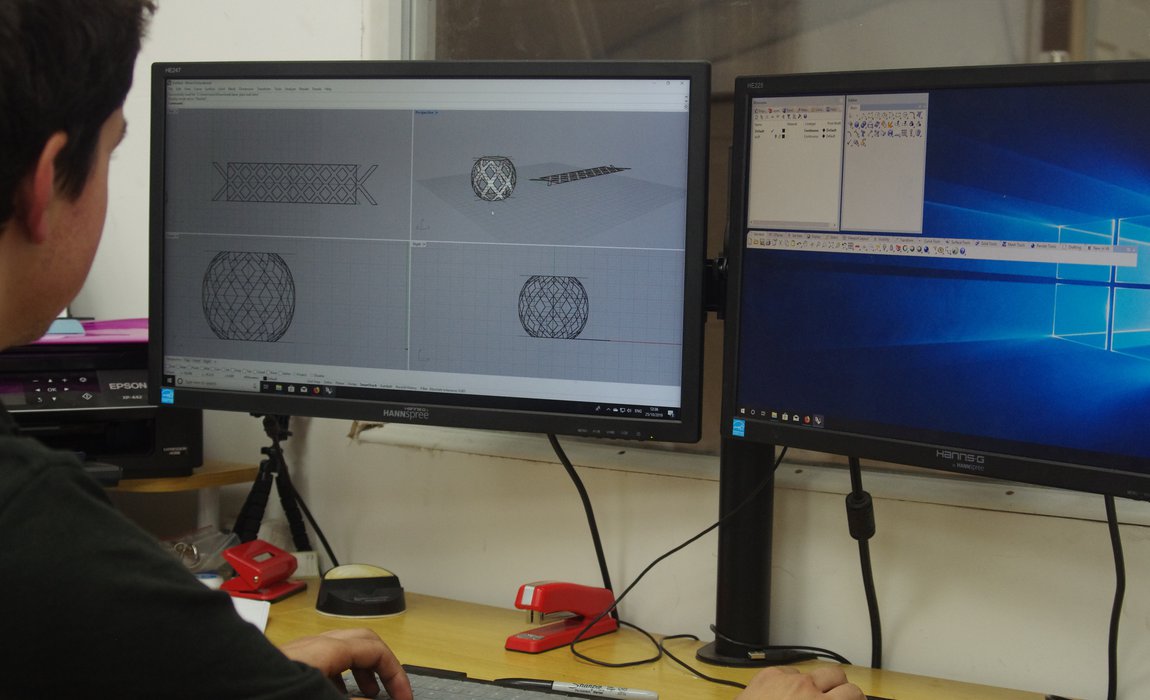
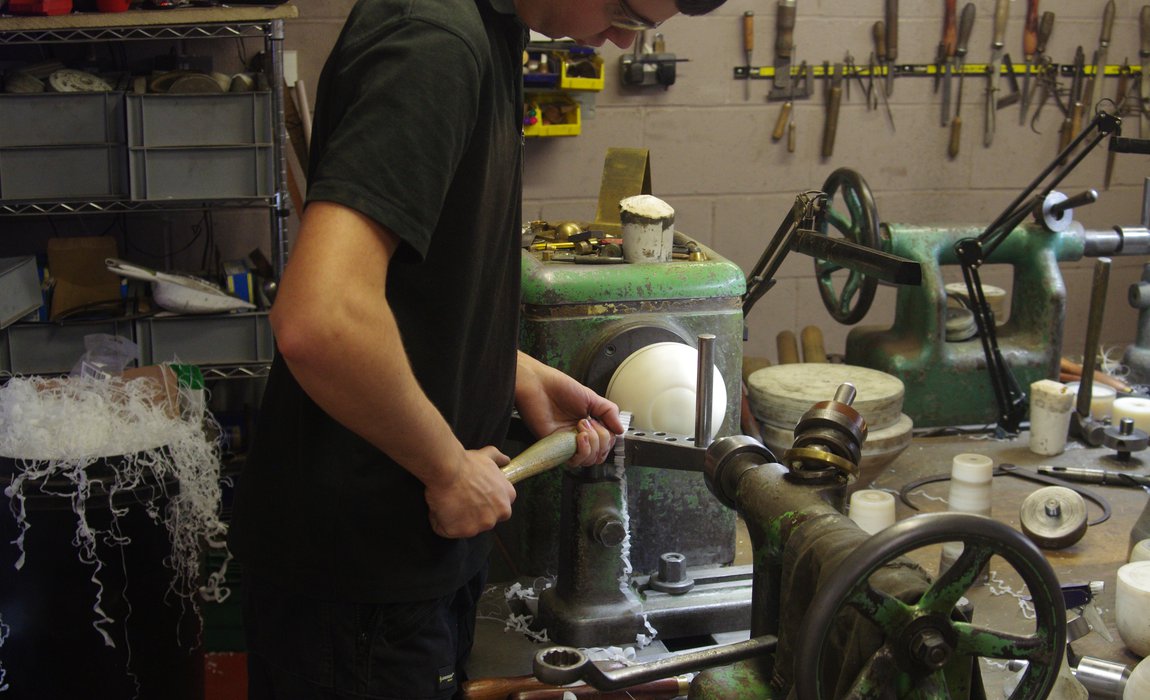
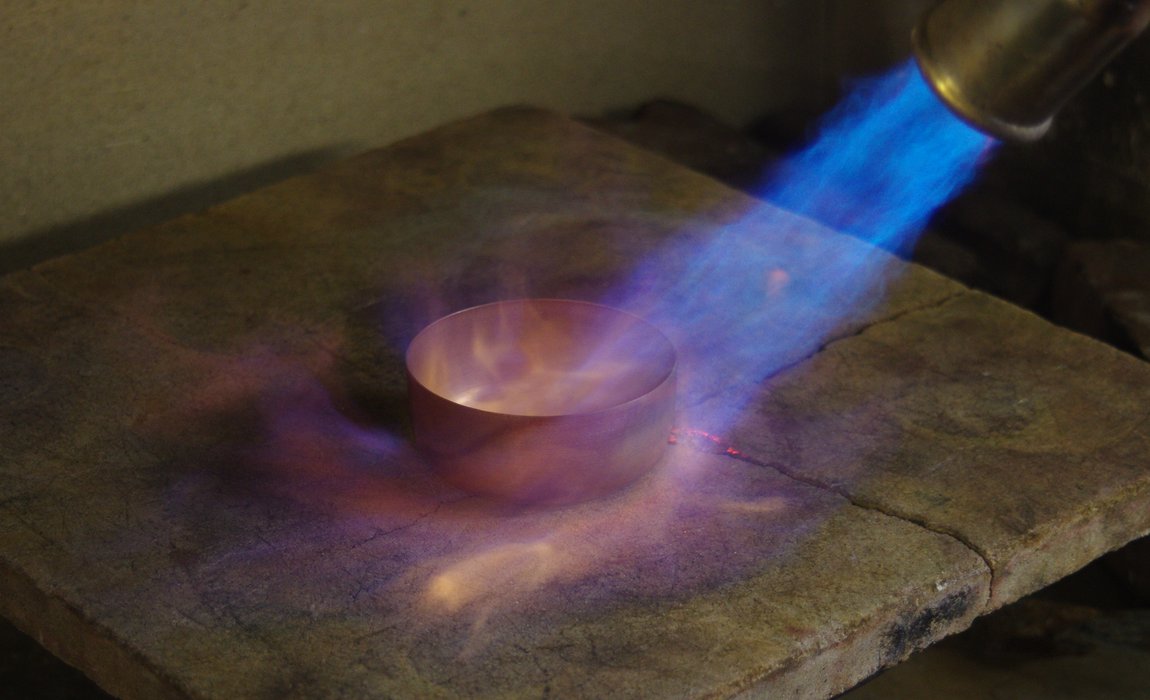
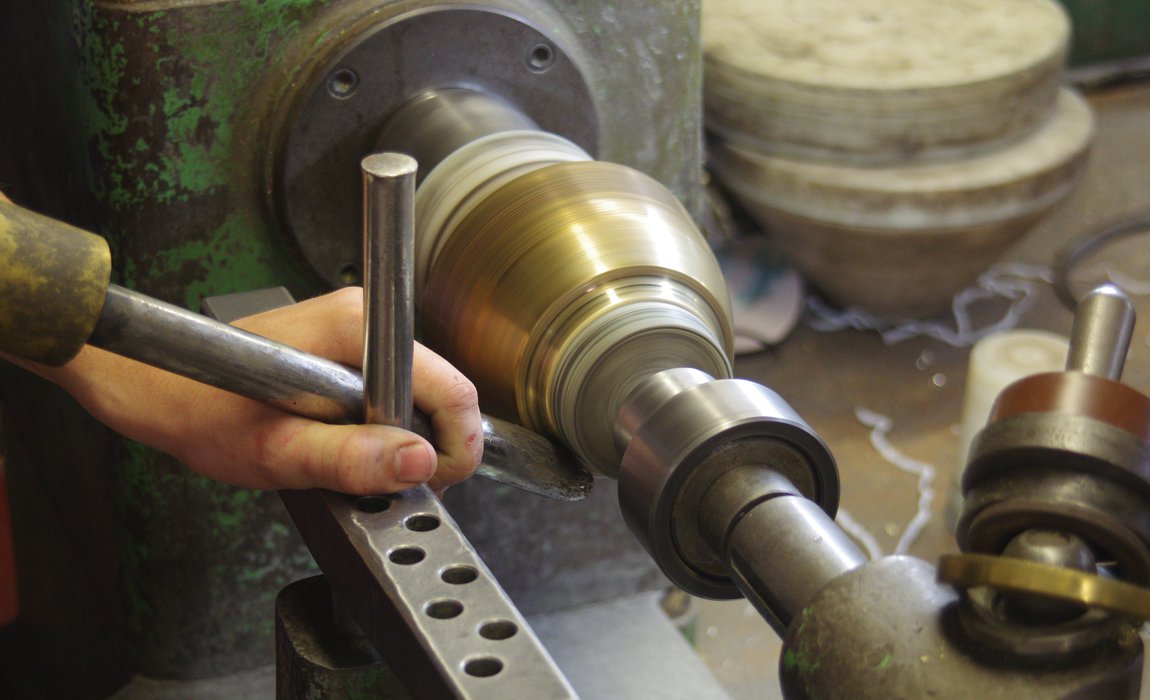
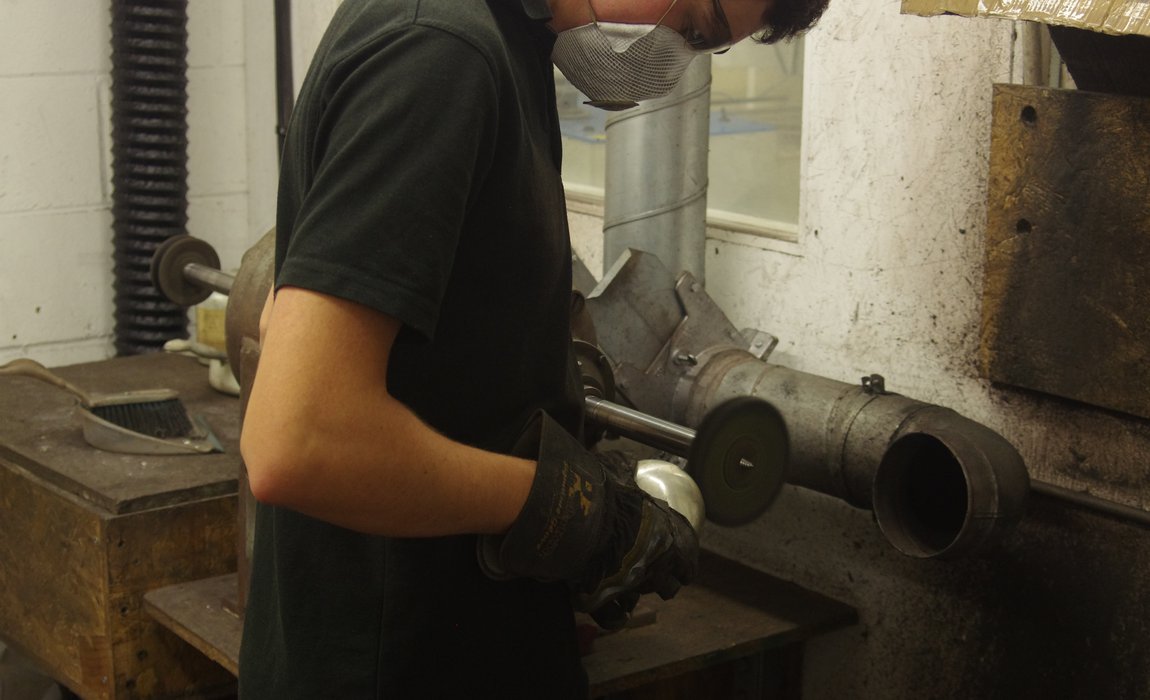
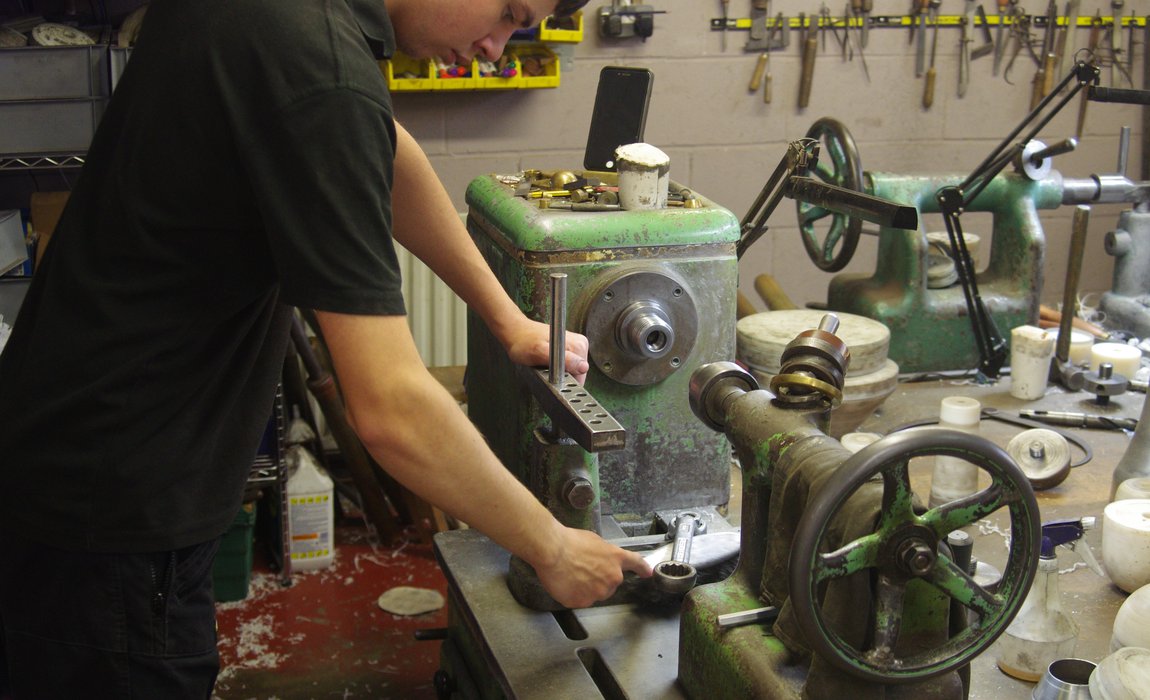
Training or qualifications: How can I become a spinner?
There are no specific academic qualifications required to become a spinner. Many specialist spinners will have completed an apprenticeship because it provides the practical training required. However, there are very few silver-spinners working right now and apprenticeships are very competitive. You could also pursue a metalsmithing degree and then gain practical experience in a workshop. Whether you pursue an apprenticeship or university degree, practical training and practice is vital.
There are several ways to start out in the jewellery, silversmithing and allied industries. To become trained as a spinner you may choose to go straight into a job, apprenticeship or relevant course at a college, university or training centre. There are very few skill-specific qualifications available, but many courses provide an introduction to a range of creative skills. To find out more about different options and your potential route into a creative career within the goldsmithing industry click here.
What can I earn as a spinner?
As an apprentice or someone who is training you should be paid at least the National Minimum Wage for your age and this rate should increase as you get closer to completing your training. Apprentices undertaking traditional training may start out earning around £12,000 – £13,000 per year and be closer to £17,000 – £18,000 at the end of their four-year apprenticeship. Once you have completed your training your earnings will vary depending on your skill and employment status.
Spinning is a niche skill and there are a limited number of practising spinners within the UK. If you are considering becoming a spinner you may wish to train in a complementary skill such as silversmithing as this will help you to understand the wider construction of pieces you may be working on.
Salaries for an employed spinner can start at around £22,000 - £25,000 per year in the first few years after training. This can rise to £28,000 - £35,000 for mid-career spinners and can reach £35,000 - £40,000 for the most experienced and skilled spinners working for a top silversmithing company.
If you are self-employed, being a spinner can be well paid if you have regular clients or constant sources of work, but it can be difficult if you are commissioned on an ad hoc basis. Due to the level of skill involved in spinning you may need to have at least 15 years’ experience becoming self-employed. As a spinner you may work to commission and will normally charge by the hour. Rates for this will depend on your experience, the materials being used, and the complexity of the piece required by the client. No matter how you work your reputation is extremely important as the goldsmithing industry often operates on word of mouth recommendations and trust.
What industry membership bodies can I join?
The Goldsmiths’ Centre offer a range of membership options for people at different stages of their career. Joining a membership body or keeping up to date with industry events allows you to create a network with like-minded individuals. They might also run workshops to acquire new skills. See for example:
The Goldsmiths’ Centre
Cockpit Arts
Contemporary British Silversmiths
Craft Central
Crafts Council
Craft Northern Ireland
Incorporation of Goldsmiths
Institute of Professional Goldsmiths
Sarabande
The Silver Society
Meet the makers
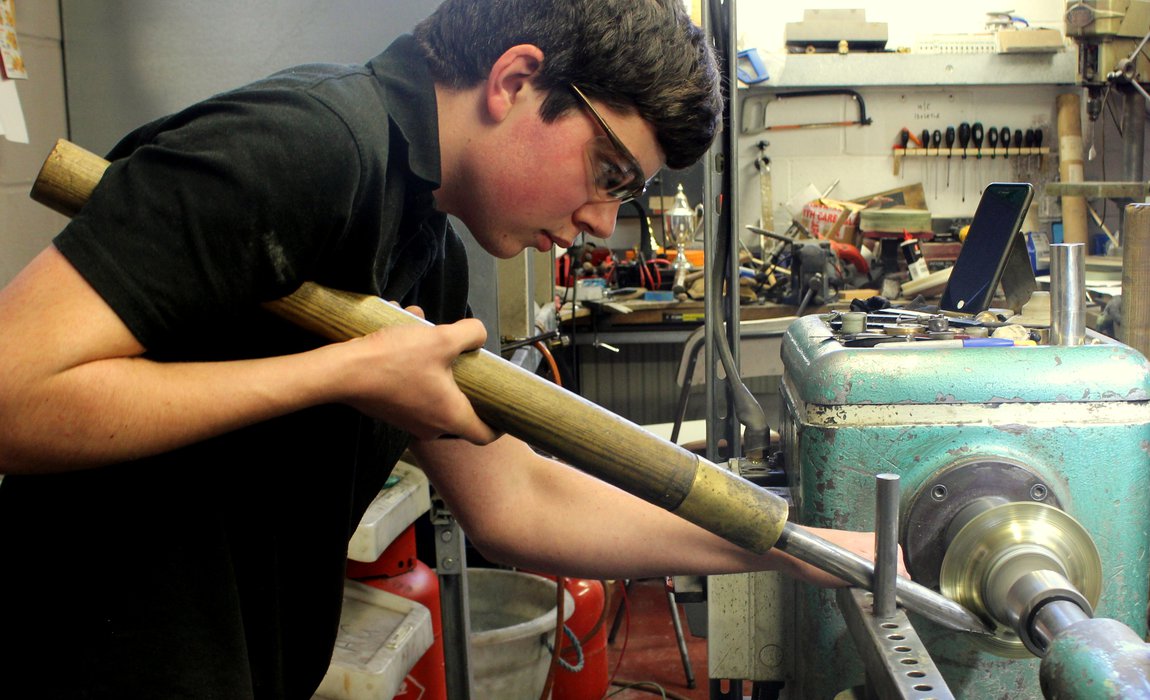
My work is very satisfying and as one of the only silver spinners in the UK, there will never be any shortage of it.
Examples of spinning
The Goldsmiths’ Company Collection includes over 8,000 pieces of antique, domestic & contemporary silver, jewellery and art medals which were made in Britain between 1350 and the present day. The Company continues to purchase, and commission pieces each year and new contemporary pieces must demonstrate innovative design combined with excellent craftsmanship. Pieces are acquired from both established craftspeople and rising stars.
The Goldsmiths’ Company also retains an image archive of Masterpieces created by apprentices in their final year on the Goldsmiths’ Company Apprenticeship Scheme. These pieces take around 350 hours to make and demonstrate the skills learnt throughout an apprentice’s training. A selection of these pieces, which demonstrate spinning, can be seen here:
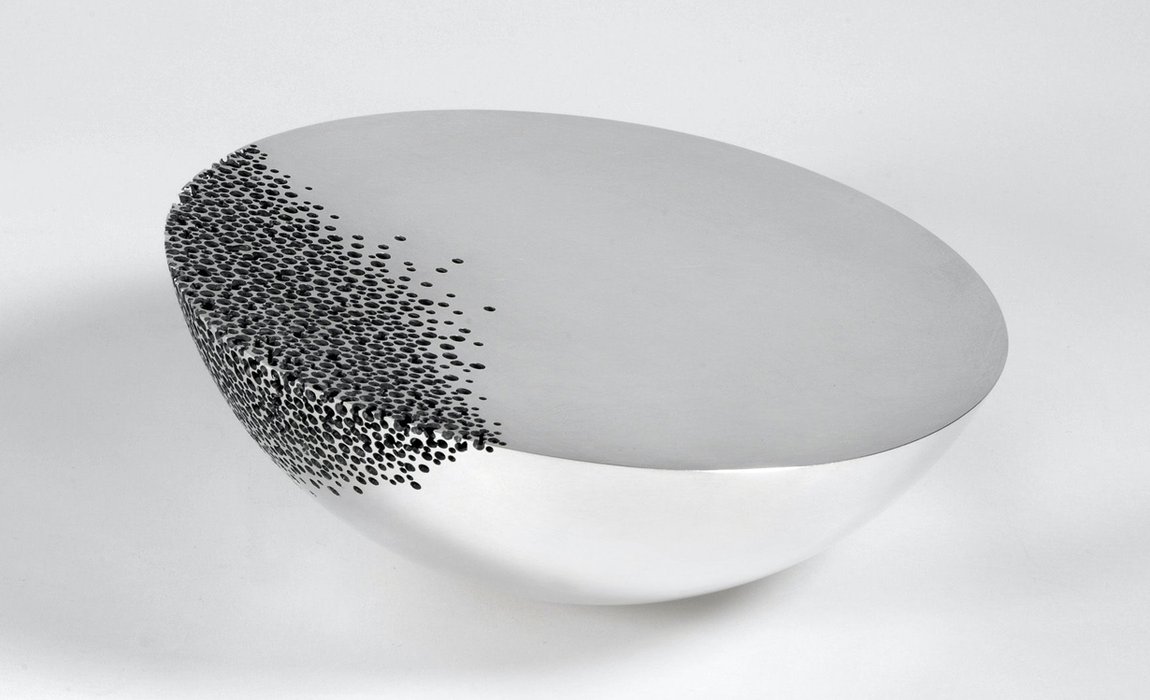
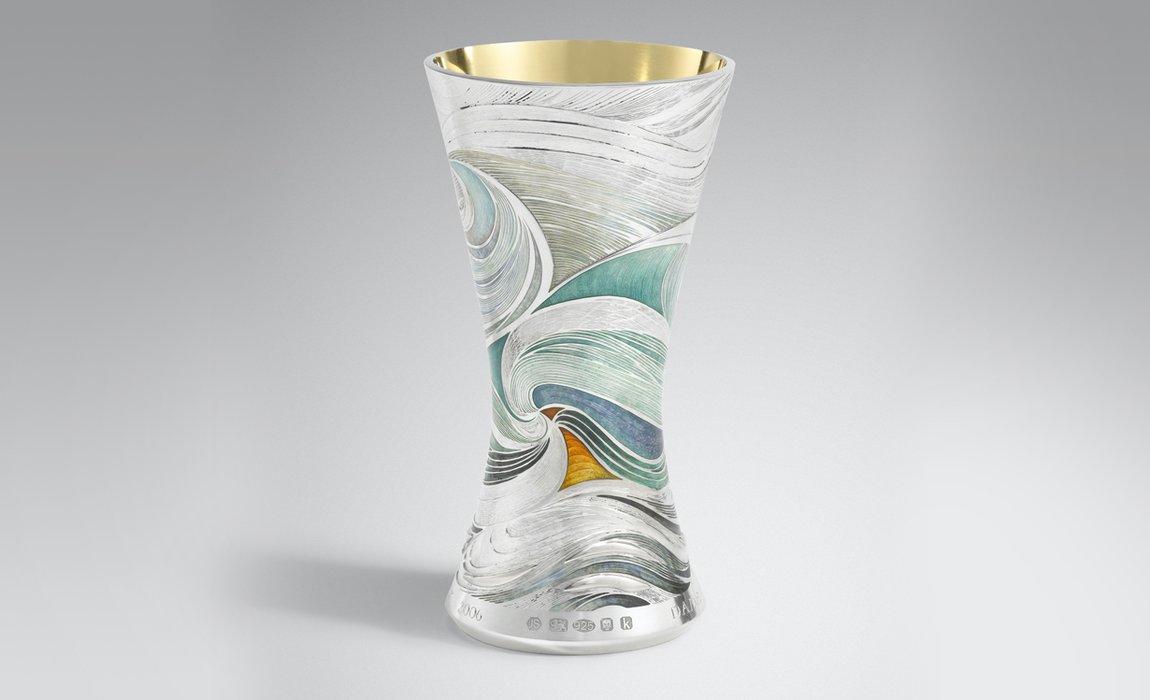
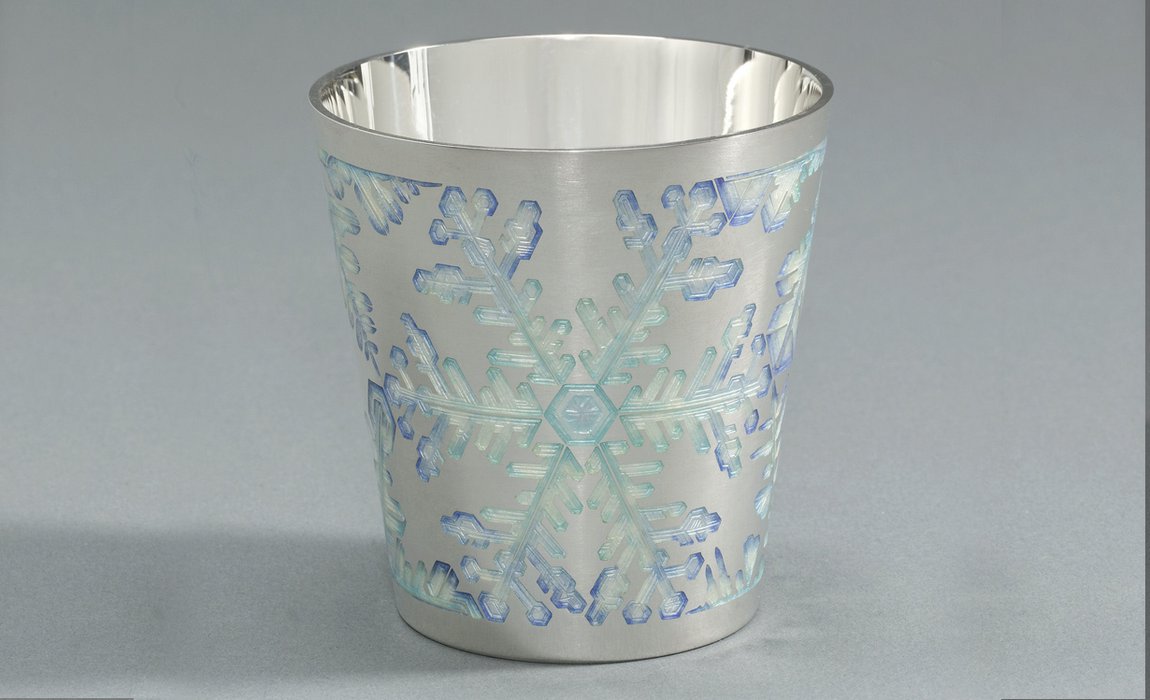
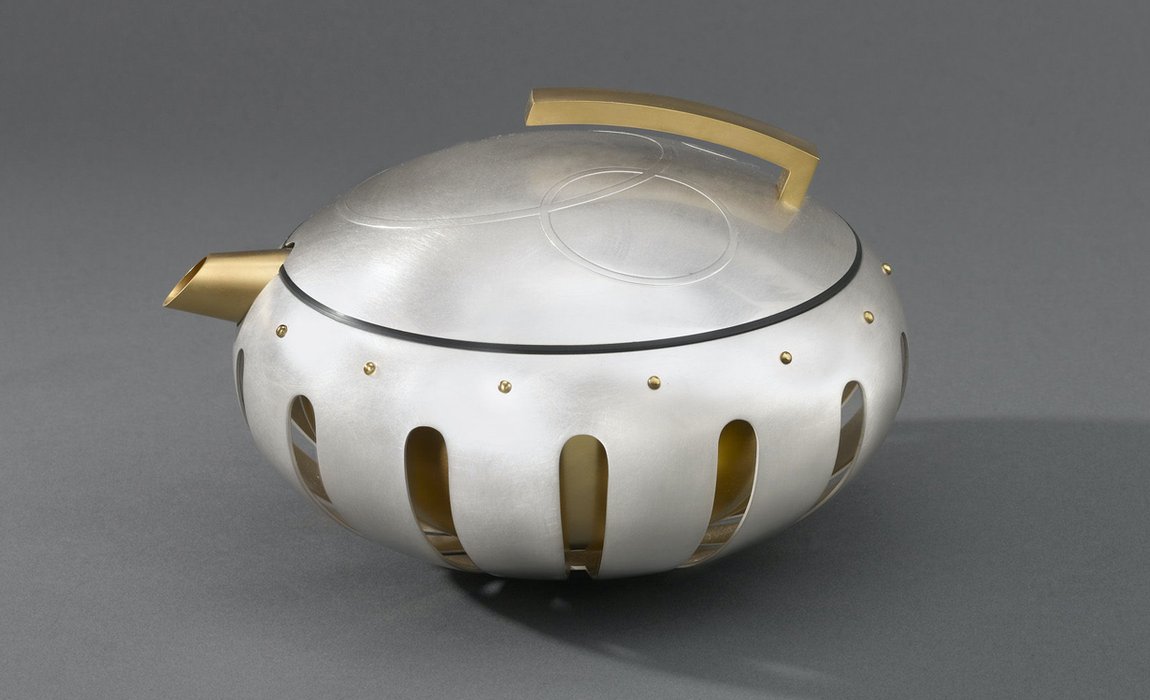
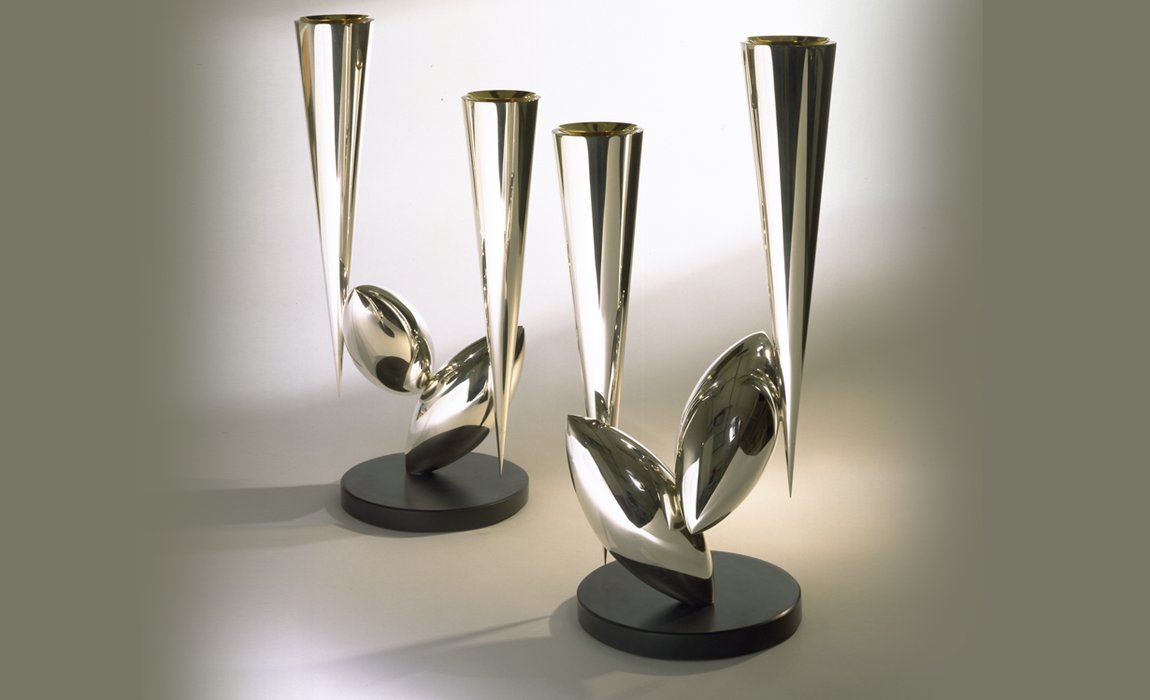

Further information
There are many reputable sources of information relating to the jewellery, silversmithing and allied industries. Whether you are trying to find information on technical skills, processes, materials, makers or inspiration some resources relating to spinning can be found below:
The Goldsmiths’ Company Library relates specifically to gold and silversmithing, jewellery, assaying and hallmarking, precious metals, and the City of London and its guilds. The Library includes 8,000+ books and 15,000+ images, magazines, periodicals and journals, technical guides, films, special research collections, design drawings produced during the early and mid-twentieth century by British or UK-based craftspeople and subject files on a wide range of industry related topics. The Goldsmiths' Company Library is also responsible for the Company’s archives, which date back to the 14th century.
Spinning related books include:
- Brian Hill and Andrew Putland, Silversmithing. A contemporary guide to making, Ramsbury, The Crowood Press, 2014
- Frances Loyen, The Thames and Hudson manual of silversmithing, London, Thames and Hudson, 1980
- Robert J.L. Martin, Working with silver: the story of a practical chemist's adventures, Pymble, NSW, Arjelem Metalcrafts, 1996