Engine Turner
An engine turner is a person who decorates the surface of metal in a fine pattern using a mechanically assisted engraving tool.
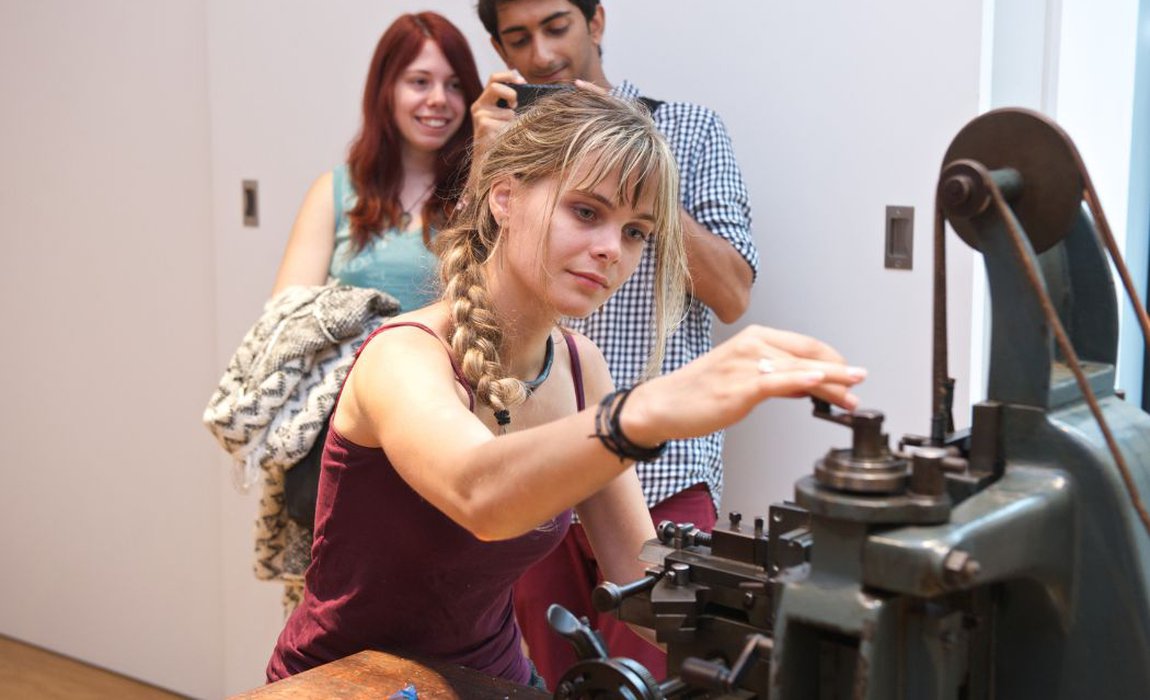
There are specific engine turning categories such as rose engine turning (repetitive geometric patterns) straight-line engine turning, round brocade engine turning (setting up a pattern to be repeated), and combined work.
“The art of engine turning, also called guilloche, was at its peak in the late 1800’s and early 1900’s and was used extensively on watch faces, jewellery and fine kitchenware.”
The art of engine turning, also called guilloche, was at its peak in the late 1800’s and early 1900’s and was used extensively on watch faces, jewellery and fine kitchenware.
What personal attributes are useful for an Engine Turner?
To be an engine turner you will need to:
- Be detail-oriented, reliable and precise
- Be able to read and interpret technical drawings
- Be able to use manual and CNC turning lathes
- Have a working knowledge of industrial machining techniques
- Be able to use measuring equipment for quality control checks
- Have a working knowledge of mechanical maintenance for machines and tools
- Have strong manual-dexterity skills
- Be able to work at both large and small scale and with different materials
Engine turners would benefit from having a silversmithing background that allows them to better understand how metal behaves. It’s also beneficial if you have experience of other technical skills such as engraving or polishing which can be used in conjunction with chasing. You need to be creative not just with your designs but with the tools you use.
What will my working life be like as an engine turner?
Engine turning machines are significant in size and are becoming increasingly rare so if you use engine turning in your work you will need significant space within your workshop. Engine turning is normally an additional skill offered by a craftsperson, rather than something you will do full-time.
As an engine turner you might be self-employed, making your own work; be an outworker producing work for someone else; or be employed by a company as part of a bigger team, earning a wage and with fixed working hours, normally from Monday to Friday. If you are self-employed you may work in your own, or a shared workshop with other craftspeople, and you may engage directly with customers to create bespoke pieces. Alternatively, you may design and sell your own pieces online, through a gallery or retail space, or directly to customers at craft fairs for example. In this case you will need to develop good business, finance, marketing and interpersonal skills too.
Within your work you must be able to adhere to industry health and safety requirements; understand the safestorage, handling and disposal of harmful materials used in the workshop including the risks involved; know how to safely operate and maintain your engine turning lathe and tools and learn how to adequately process your materials, including historic pieces. As engine turning is a rare skill, you may be likely to work on restoring historic pieces of work. Understanding how these pieces were made, how to work with lathe(s) and related equipment works and how to maintain them will be key. As an engine turner you will use skills and techniques including decorating items in accordance with verbal or written instructions to the dimensions given, interpreting and executing working drawings; have the ability to work out what materials are required for your project; know the specific uses of different types of lathes and how to work with each to achieve the desired result; be able to avoid common pitfalls within your work; and know how to finish resulting metal pieces.
You will find it useful to maintain a working knowledge of the history and tradition of jewellery, and silversmithing as a main source of engine turning work may come from historic restoration of pieces. You can expect to work with different types of engine turning lathes and a wide range of historic materials. In order to produce new items to be engine turned you will benefit from having a working knowledge of silversmithing, diamond mounting and engraving techniques. You should receive training in all of these as required.
A day in the life of an engine turner
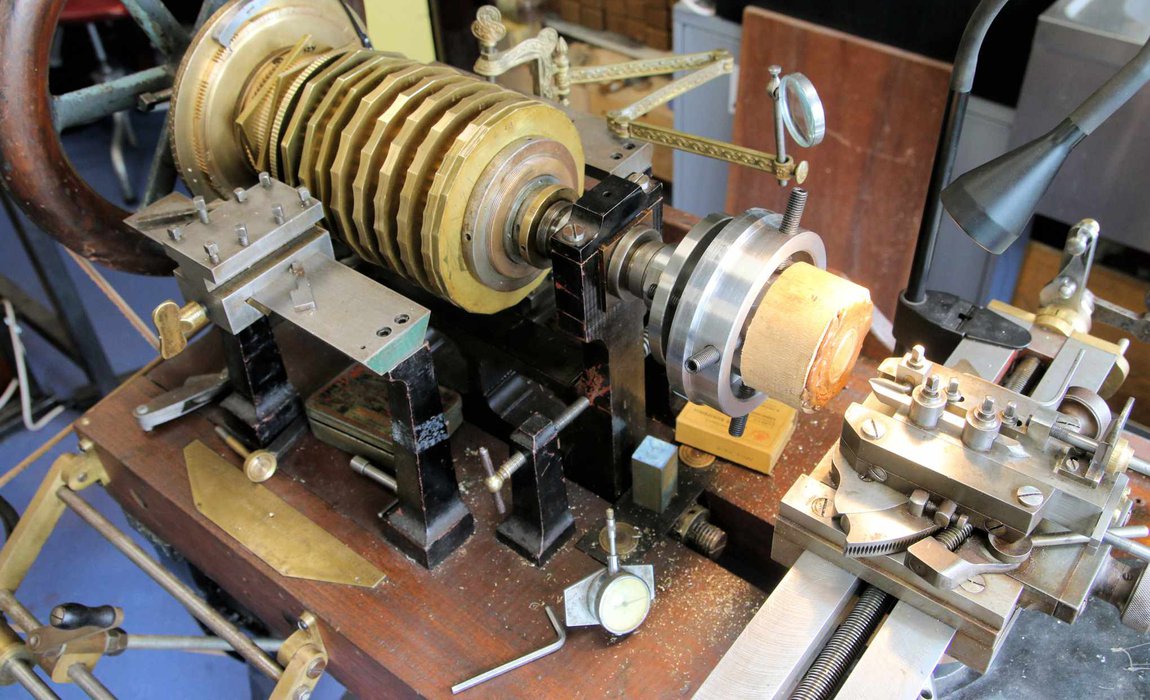
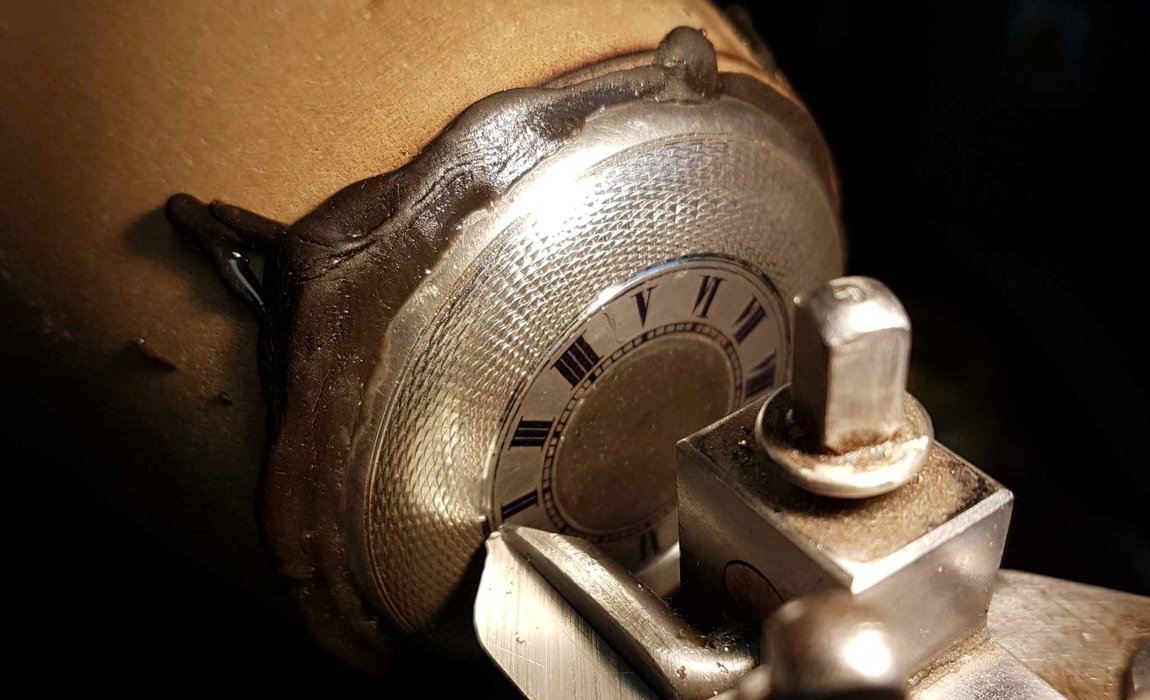
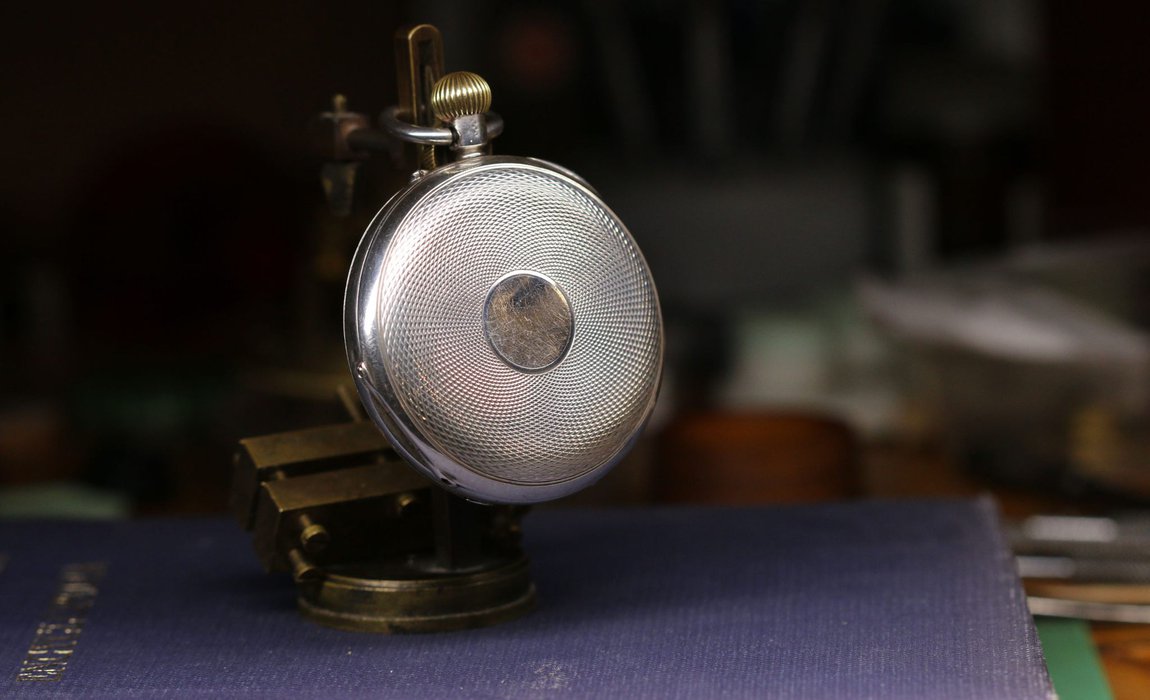
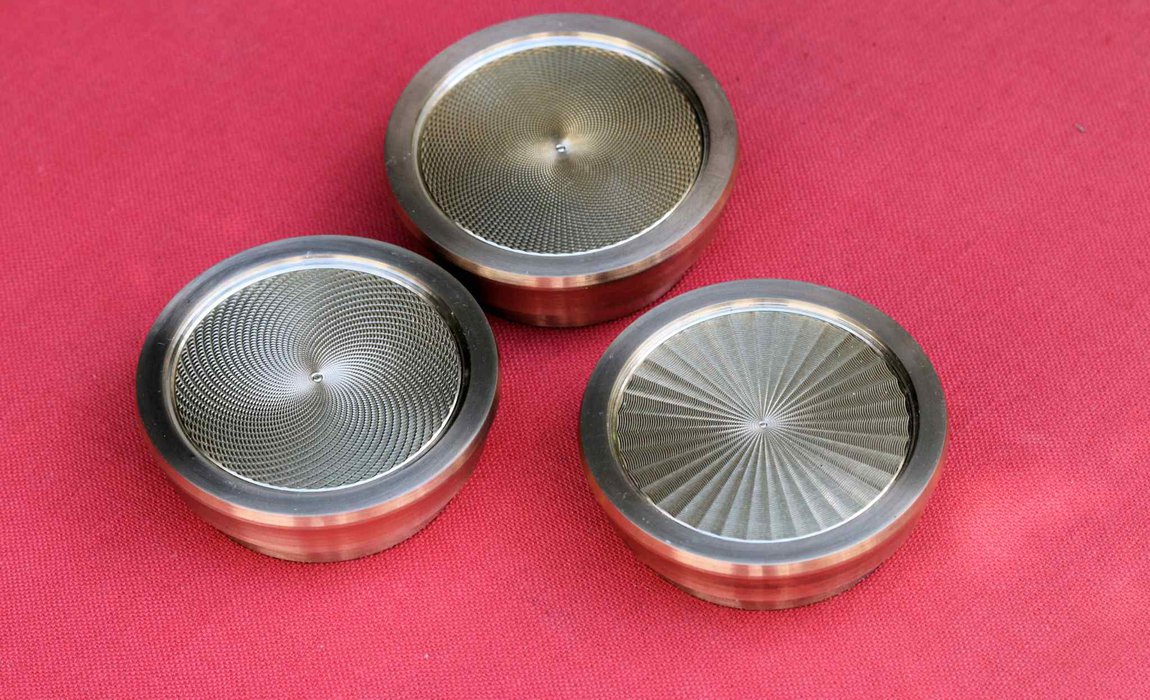
Training or qualifications: How can I become an engine turner?
There are several ways to start out in the jewellery, silversmithing and allied industries; you may choose to go straight into a job, an apprenticeship or relevant course at a college, university or training centre. There are very few skill-specific qualifications available, but many courses provide an introduction to a range of creative skills. To find out more about different options and your potential route into a creative career within the goldsmithing industry click here.
Engine turning is classed as a critically endangered heritage skill and there are very few practising craftspeople and engine turning lathes in the UK. In order to learn how to engine turn you may need to do detailed research in order to find someone who is able to teach you. Have a look at the Heritage Craft Association or look into restoration training as a start point.
What can I earn as an engine turner?
As an apprentice or someone who is training you should be paid at least the National Minimum Wage for your age and this rate should increase as you get closer to completing your training. Apprentices undertaking traditional training may start out earning around £12,000 – £14,000 per year and be closer to £18,000 – £20,000 at the end of their four-year apprenticeship. Once you have completed your training your earnings will vary depending on your skill and employment status.
If you are self-employed, being able to offer engine-turning as a skill could be well paid if you have regular clients who require this. As engine turning is no longer well known, it may be difficult to find work if you are commissioned ad hoc. As an engine turner you may work on a commission basis and agree a fee per job, per hour or per day. Rates for this will depend on your experience, the materials being used, and the complexity of the piece required by the client. No matter how you work your reputation is extremely important as the goldsmithing industry often operates on word-of-mouth recommendations and trust.
What industry membership bodies can I join?
The Goldsmiths’ Centre offers a range of membership options for people at different stages of their career. Joining a membership body or keeping up to date with industry events allows you to create a network with like-minded individuals. They might also run workshops to acquire new skills. See for example:
- The Goldsmiths’ Centre
- Association for Contemporary Jewellery
- British Society of Enamellers
- Cockpit Arts
- Contemporary British Silversmiths
- Craft Central
- Crafts Council
- Craft Northern Ireland
- Guild of Enamellers
- Hand Engravers Association of Great Britain
- Heritage Craft Association
- Incorporation of Goldsmiths
- Institute of Professional Goldsmiths
- National Association of Jewellers
- Sarabande
- Scottish Mineral & Lapidary Club
- Society of Jewellery Historians
- The Silver Society
- The Society of Ornamental Turners
- The Worshipful Company of Turners
Images of work (including from Goldsmiths’ Company Collection):
The Goldsmiths’ Company Collection includes over 8,000 pieces of antique, domestic & contemporary silver, jewellery and art medals which were made in Britain between 1350 and the present day. The Company continues to purchase, and commission pieces each year new contemporary pieces must demonstrate innovative design combined with excellent craftsmanship. Pieces are acquired from both established craftspeople and rising stars, and a selection of these pieces, which demonstrate engine turning, can be seen here:
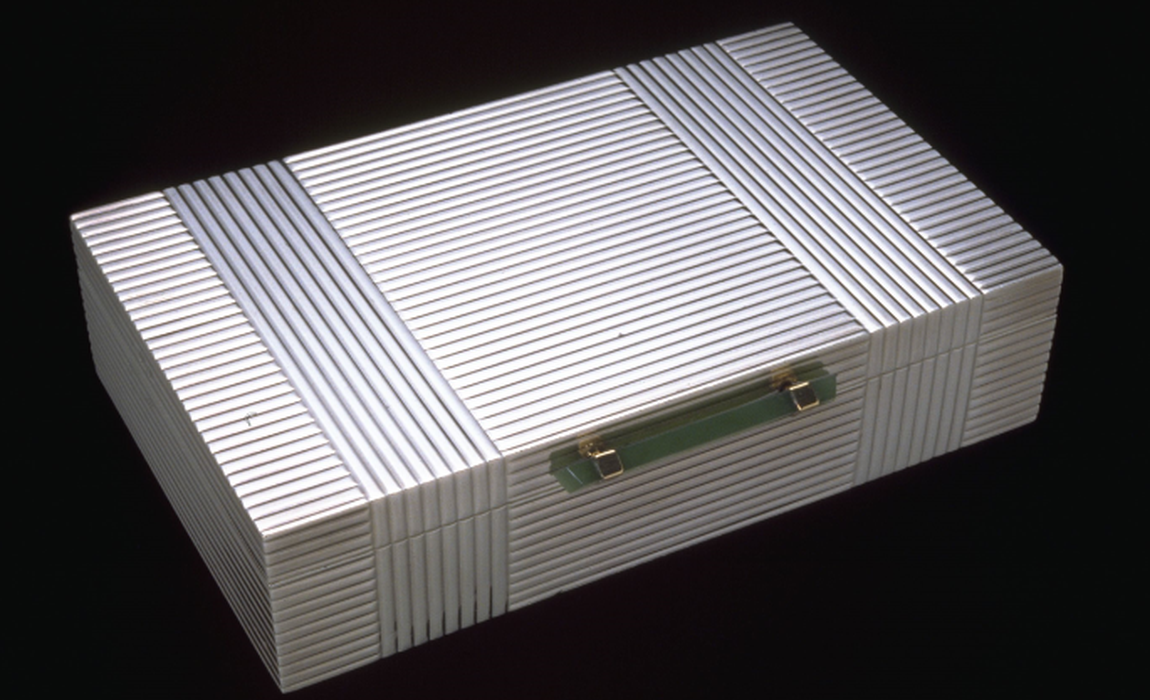
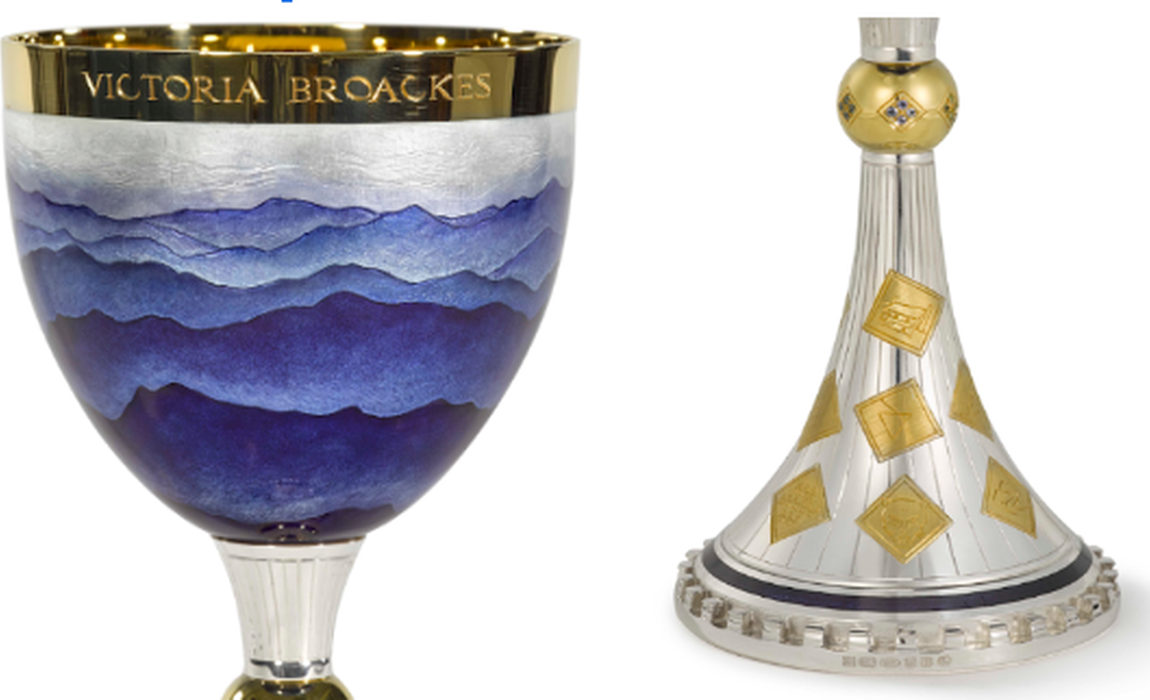
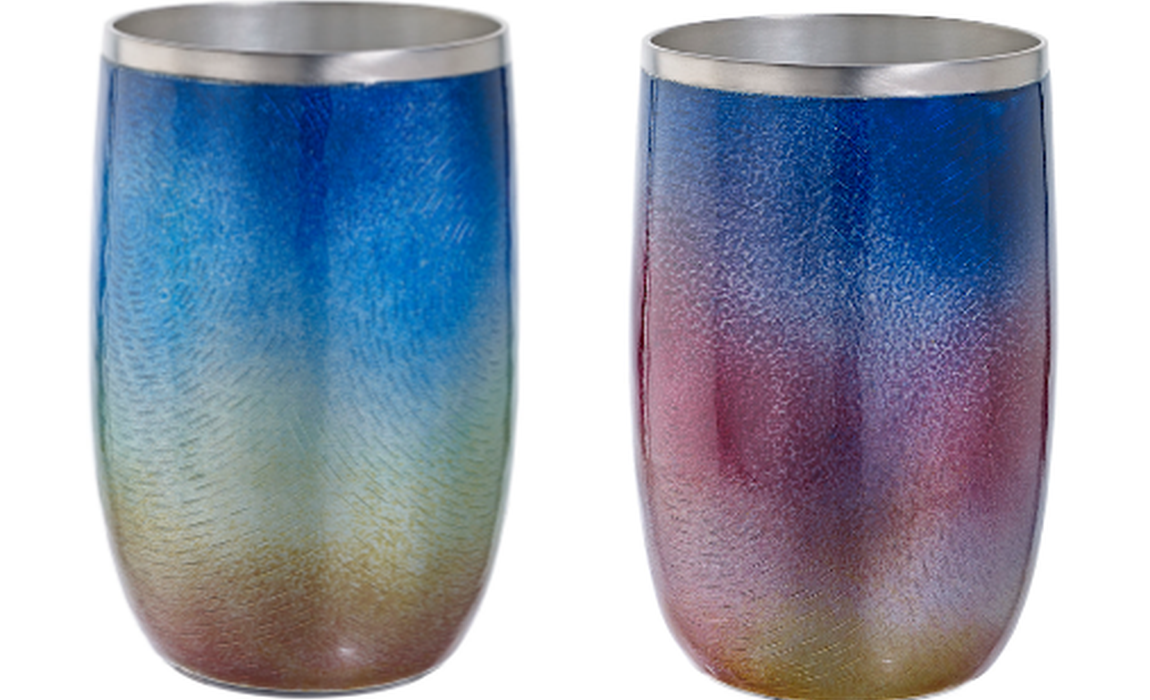

Further Information
There are many reputable sources of information relating to the jewellery, silversmithing and allied industries. Whether you are trying to find information on technical skills, processes, materials, makers or inspiration some resources relating to engine turning can be found below:
Engine turning related books or archived materials include:
- Martin Matthews, Engine turning 1680-1980 : the tools and technique, Sevenoaks, Private Print, 1984.
- Andreas Gut and Gutfrieda Dörfer, (eds), Embossing, Punching, Guilloché engraving: Contemporary Artisanal Jewellery Production, Stuttgart, Arnoldsche, 2017.
Engine turning related articles include: