On Your Marks: The Development in Assay Office Marking Technology
Hallmarking of precious metal items was established around 700 years ago. Since then there have been huge changes in legislation, the materials we use and how the hallmark is applied. This article outlines the more recent changes in how laser technology has had an impact.
How are hallmarks applied?
The traditional method of applying marks which make up the UK hallmark is with a punch. While it might appear straightforward to apply such a mark nothing could be further from the truth. If the article is not supported correctly with appropriate tooling, and the amount of force used is not right, then the metal around the mark will become badly distorted or ‘bruised’. Much of the intellectual property of an Assay Office thus rests around minimizing such bruising through effective tooling design and ensuring high skills of the marker. Most Assay Offices retain extensive engineering workshops and have training programs, such as apprenticeships, to ensure that skills are handed down from one generation to the next.
“Customers still like the association of hand-crafted quality that striking a mark with a punch entails – the marks on any two articles are never quite the same, making each article unique.”
How do Assay Office produce marking punches?
The quality of the punch clearly has a huge bearing on the final quality of the mark. Early punches were made by direct engraving onto a punch blank or by ‘hobbing’; stamping an impression of one punch on to a blank with another punch. More consistency between batches was introduced by pantograph engraving. A pantograph engraving machine comprises two arms mechanically linked in the manner shown in Image 1.
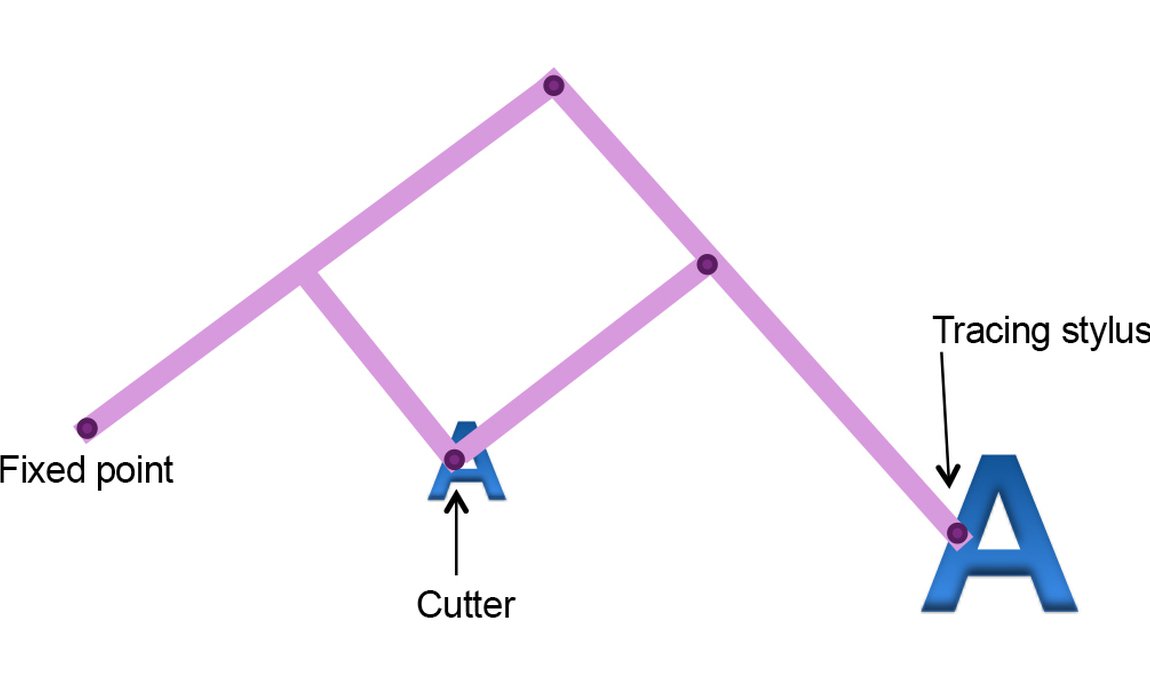
One arm of the machine comprises a fine stylus which traces the surface of a stencil, in this case an enlarged ‘master copy’ of the mark to be applied. The other arm is connected to a rotating cutting blade, which engraves a miniature but otherwise perfect copy of the master on the surface of the punch. Different sizes can be produced by changing the geometries of the arms in the pantograph. The tracing process requires considerable skill by the operator to ensure that all the detail is captured.
Once the engraving is completed, the ‘shoulders’ of the punch are filed by hand up to the edge of the shields around the mark. With shield sizes ranging from 6mm down to 0.3mm, this is another highly skilled operation. The engraving and hand finishing processes are carried out in a softened state. The punch is hardened then tempered and water quenched to create the required surface hardness.
How is laser marking different?
In the late 1990s, lasers were introduced for marking, and have had a major impact on hallmarking. Unlike punch marking where material, within the finished piece, is moved to create the desired mark impression, laser marking is an engraving process where material is removed from the surface as shown in Image 2.
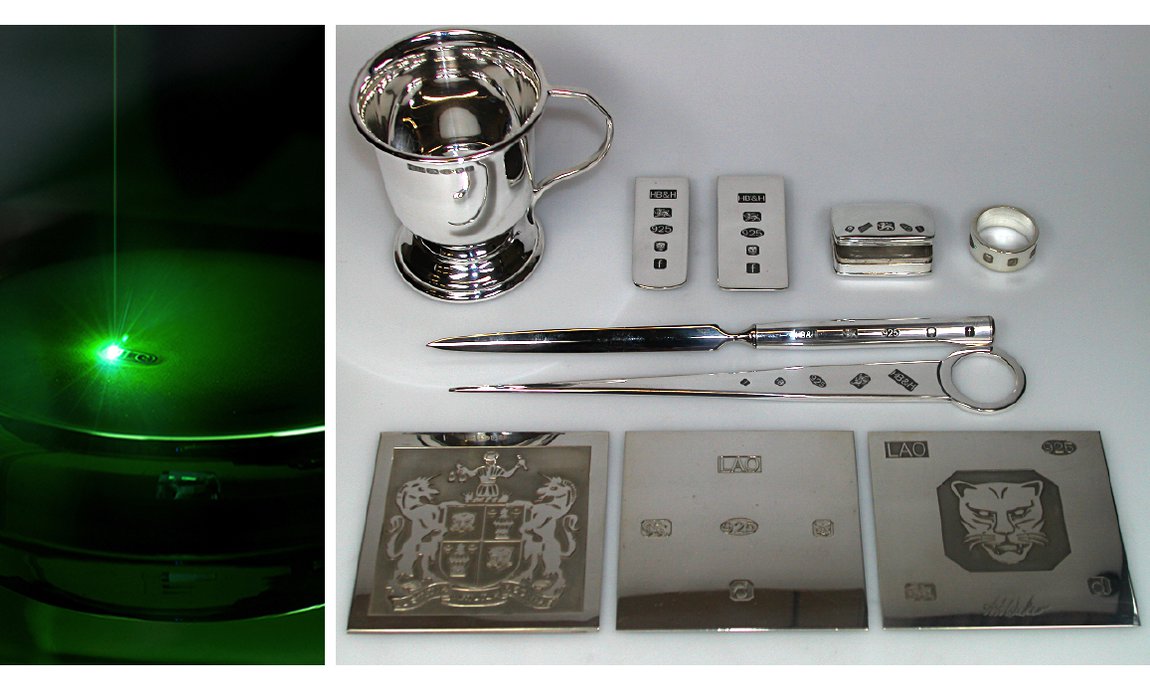
This immediately eliminates any potential for bruising, making it ideal for hollow or delicate items. It has proved highly useful for marking finished items as no remedial work or ‘setting back’ of bruised marks are required. Lasers can produce marks which resemble struck marks or produce outline marks that give excellent definition when applied to small articles as can be seen in Image 3 where struck, deep laser and outline marks are shown for comparison. They are also useful for applying logos or signatures.
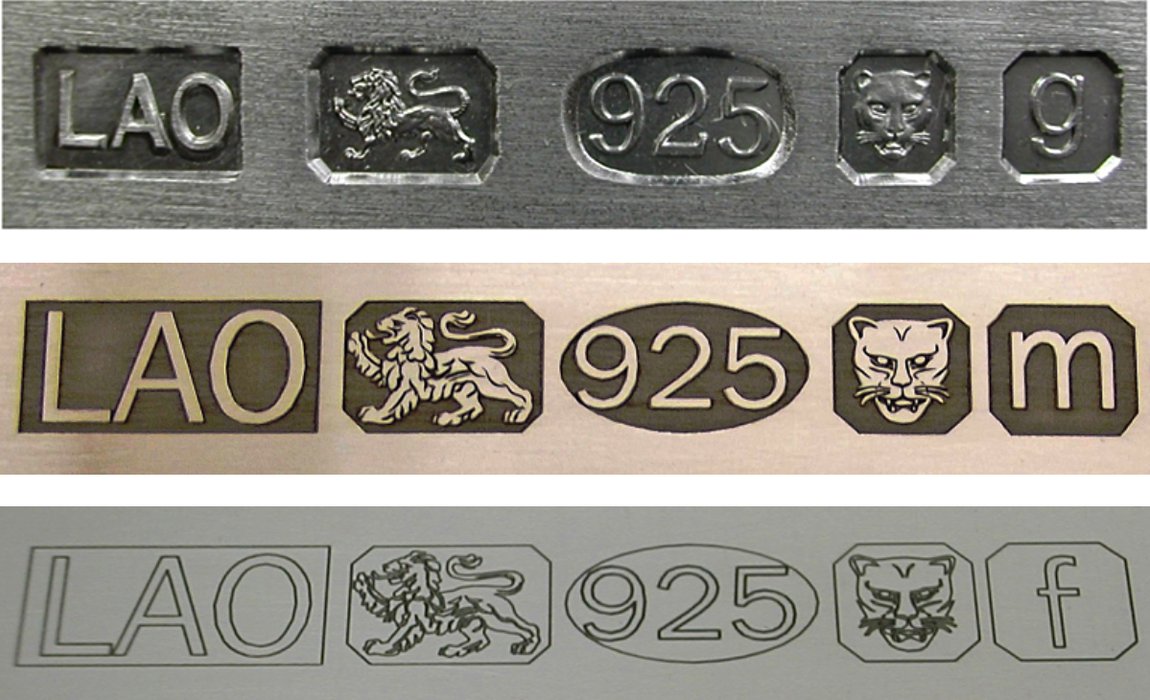
How does laser marking work?
The ability to generate the detail in the engraved surface with a laser is achieved by selective removal of material in layers. If sufficiently small layers are taken, smooth, 3D features are created in the surface. The layers of the pattern are removed using a fine laser beam which pulses on and off, passing across the surface of the article as demonstrated in Image 4. The rastering process uses a spinning mirror, within the scan head, to accurately direct the laser, ensuring accuracy in the cutting.
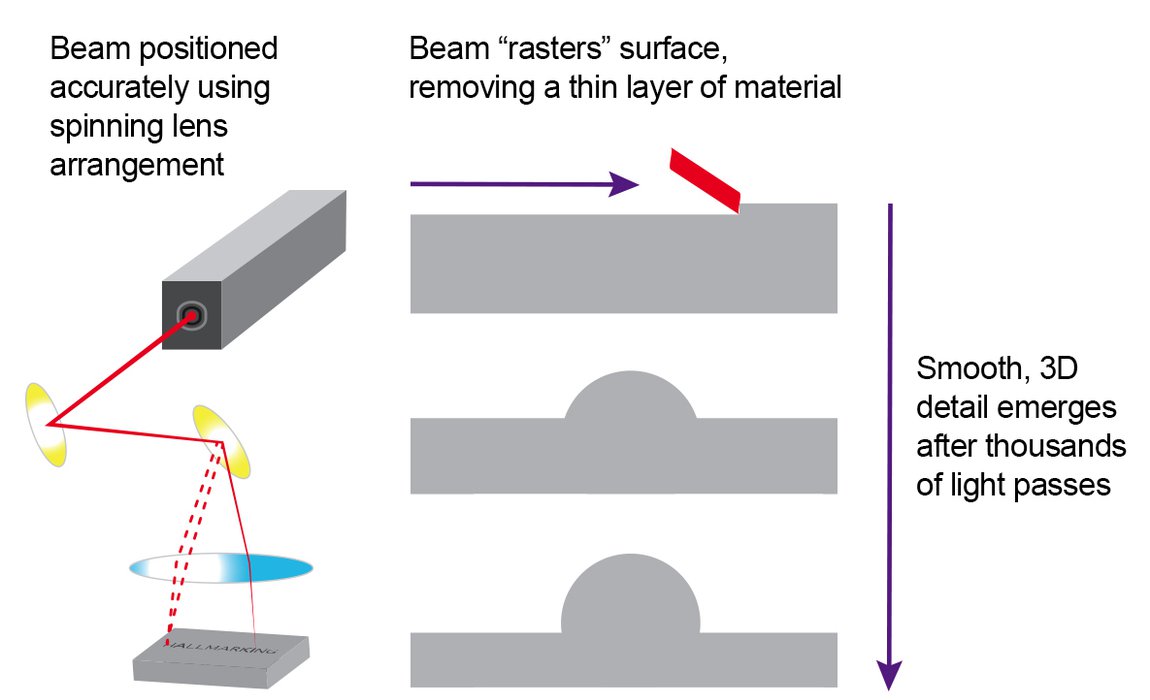
The technology used in the laser has changed significantly since lasers were first introduced for hallmarking. In particular, it is the gain medium (a crystal or optical fibre) and the source used to pump the gain medium which have changed. As each new technology has been introduced, there has been an increase in resolution and reliability. Machines have also become more compact and convenient.
The latest technology keeps the use of a diode as the source but replaces the crystal gain medium with an optical fibre doped with elements, such as ytterbium. A very stable beam is produced. Less complicated optical arrangements are necessary due to the fine diameter of the fibre, creating better resolution. Less energy is also needed as the beam is created along the long length of the fibre. Air cooling is sufficient, resulting in simpler, more compact machines. A summary of the advancement in laser technology is shown in Image 5.
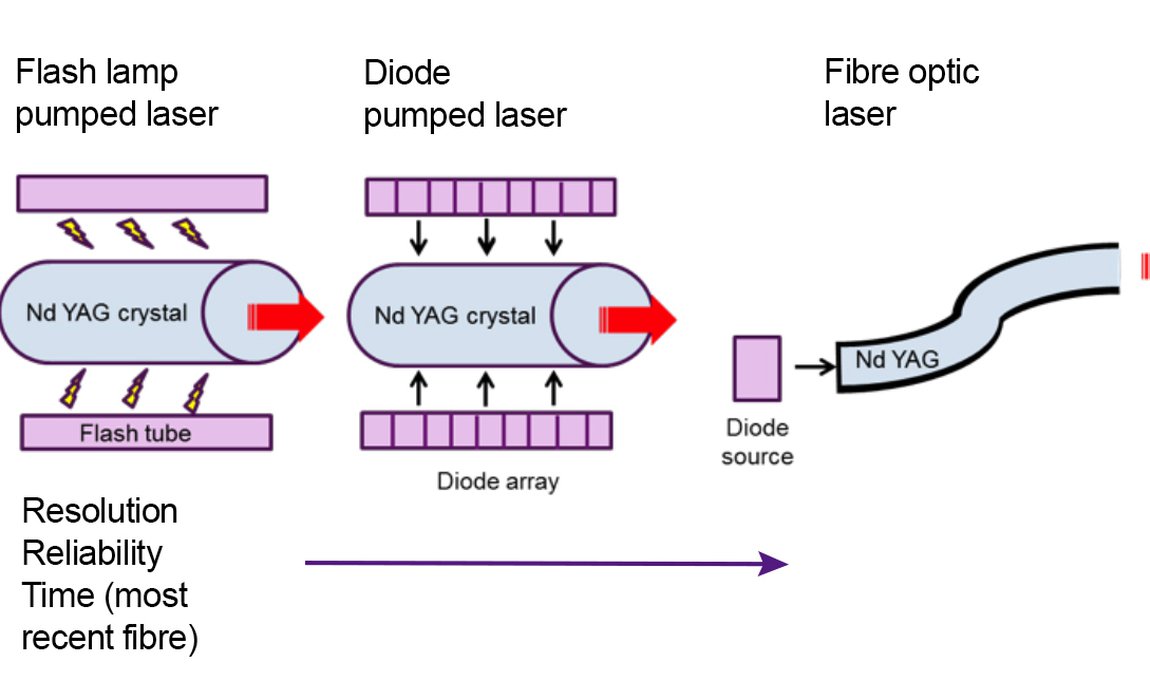
And how are lasers being used to produce more accurate punches?
Once the use of lasers had been established for marking, it seemed an obvious step to use the technology for punch making. However, while the principle of the etching process is the same, punch manufacture is significantly more demanding than for marking. The designs for punches are more complicated because a ‘release angle’ needs to be incorporated to allow the punch to be removed easily after striking the article. In addition, the finish of the 3D features in the etched surface must be considerably smoother as the slightest amount of roughness will ‘pull out material’ when the punch is removed.
There must also be no residual or re-deposited etched material (recast) trapped in the details. Lasers used for punches must have higher layer depth control as many more passes need to be given to create the smoothest features. Also, as there are more layers, greater control of the beam profile and pulse frequencies are required to ensure the correct power is given to remove sufficient material, while preventing excessive melting of the surface (which reduces resolution) and to prevent recast.
(See also On Your Marks…How the London Assay Office produces hallmarking punches using laser technology article)
Conclusion and further information
In summary, it could be said that the hallmarking process is carried out by lasers because lasers are used for both marking directly and the making of punches! The question that could be asked is why laser marking is not used for hallmarking all articles. Indeed, it is in some countries which have recently introduced hallmarking systems. However, in the UK, uptake has been no more than around 20% of all items hallmarked. This is because customers still like the association of hand-crafted quality that striking a mark with a punch entails – the marks on any two articles are never quite the same, making each article unique.
There are many reputable sources of information relating to the jewellery, silversmithing and allied industries. Whether you are trying to find information on technical skills, processes, materials, makers or inspiration some resources relating to hallmarking can be found below:
The Goldsmiths’ Company Library relates specifically to gold and silversmithing, jewellery, assaying and hallmarking, precious metals, and the City of London and its guilds. The Library includes 8,000+ books and 15,000+ images, magazines, periodicals and journals, technical guides, films, special research collections, design drawings produced during the early and mid-twentieth century by British or UK-based craftspeople and subject files on a wide range of industry related topics. The Library is also responsible for the Company’s archives, which date back to the 14th century.
Hallmarking related articles include:
- Industry Profile: Assay Office Technician
- On Your Marks…How the London Assay Office produces hallmarking punches using laser technology
Author: Dr Robert Organ, Deputy Warden of The Goldsmiths’ Company